铝材切削液使用中腐蚀、黏结、材料变形等问题解决方案
作者: 佳润润滑油 发布时间:2024:10:24 阅读量:64次
腐蚀问题是铝材切削加工中最为显著的问题之一。铝材在弱酸或强碱环境下均易发生腐蚀,因此,切削液的pH值控制成为关键。建议将切削液的pH值维持在8.2至9.5之间,这一范围既能有效防止铝材的化学腐蚀,又能保持切削液的性能稳定。此外,添加铝缓蚀剂是预防腐蚀的有效手段,缓蚀剂能在铝材表面形成一层保护膜,隔绝切削液与铝材的直接接触,从而减缓腐蚀过程。值得注意的是,切削液中的碱性添加剂在铝工件表面风干后可能产生黄斑,这也是一种腐蚀现象。因此,在选择切削液时,应优先考虑低泡、低残留的产品,并在加工后及时清洗工件,避免残留物对铝材的进一步侵蚀。
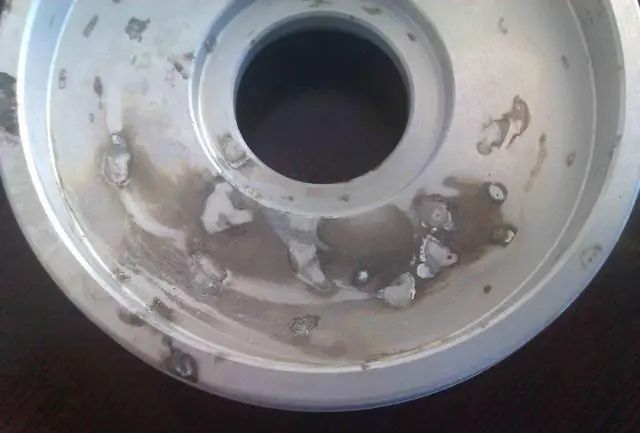
黏结问题主要源于铝合金的柔韧性,使得切削过程中产生的铝质颗粒容易黏附在刀具表面,形成积屑瘤,增加切削阻力,降低加工效率。为解决这一问题,可采用高润滑性的切削液,减少刀具与工件之间的摩擦,降低积屑瘤的形成。同时,选择适当的切削参数,如降低切削速度、增加进给量,也能在一定程度上减轻黏结现象。对于材料变形,铝合金的高热膨胀系数使得加工过程中产生的热量迅速传导至工件,导致尺寸难以控制。因此,除了选用具有良好冷却性能的切削液外,还应优化冷却系统,确保切削液能够充分覆盖并带走加工区域的热量。此外,采用预冷或后处理技术,如冷却液喷淋、工件浸泡等,也能有效减少热变形。
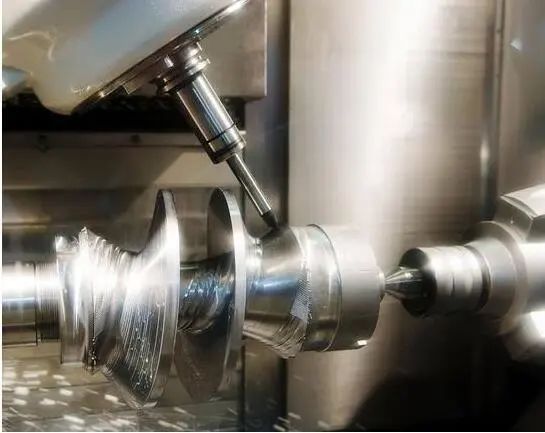
泡沫问题主要由切削液中的乳化剂和活性成分引起,过多的泡沫会干扰操作视线,影响加工精度。控制泡沫的方法包括调整水质硬度、添加消泡剂以及优化切削液配方等。其中,添加适量的消泡剂是快速有效的解决方法,但需注意消泡剂与切削液的兼容性,避免产生新的化学问题。细菌侵蚀是切削液长期使用中不可避免的问题。细菌在切削液中繁殖,会导致pH值下降,影响切削液的防锈和防腐性能。为防止细菌滋生,应定期向切削液中添加杀菌剂,并保持切削液的浓度和清洁度。同时,建立完善的切削液管理制度,包括定期更换、过滤和清洗系统,也是预防细菌侵蚀的重要措施。
铝屑问题是铝材切削加工中常见的难题。切削下来的铝屑轻而细小,难以沉淀,容易随切削液循环进入加工区,划伤工件表面。为解决这一问题,应选用高效的过滤系统,确保切削液中的铝屑得到有效去除。此外,定期清理切削液槽和管道,防止铝屑积累,也是保持加工环境清洁的关键。切削液的定期维护同样重要。应定期检查切削液的浓度、pH值和细菌数量,并根据实际情况进行调整和补充。当切削液性能下降或污染严重时,应及时更换新液,避免对加工质量和设备造成不良影响。铝材切削液在使用过程中面临的挑战多种多样,但通过科学的配方设计、合理的使用方法和严格的维护管理,这些问题都可以得到有效解决。企业应根据自身加工需求和实际情况,选择合适的切削液产品,并建立完善的切削液管理制度,以确保加工质量和生产效率的稳定提升。同时,随着技术的进步和环保要求的提高,未来切削液将朝着更加环保、高效、智能的方向发展,为铝材加工行业带来更多创新和机遇。